Introduction
Cardboard box manufacturers are one of the most useful packaging materials available on today’s market. They provide simplicity, portability and flexibility, which makes them ideal for the packagin box manufacturers industry.
Some suppliers not only deliver ingredients to retailers, but also supply ingredients directly to manufacturers.
Cardboard boxes are usually printed with graphics and text that make them look attractive. When you see a cardboard box, box manufacturers hard to imagine that those same boxes started out as trees.
Here, we walk you through each step that box manufacturers take to make custom cardboard boxes.
The Steps of Box Manufacturing
Below is a step-by-step process involved in making the cardboard boxes:
- The Tree
Cardboard boxes are often made from recycled materials, but sometimes new cardboard is made from trees. In general, softwood trees such as pine and fir trees are used to make boxes.
The reason for using them is that they have the longest fibers of any paper product. These fibers help create a smooth surface for the cardboard and increase strength by creating tension in the material.
Many manufacturers use wood from sustainably managed forests; that means any trees that are felled are replaced to help maintain the forest’s ecosystem.
There will be a difference in the coloring of paper and cardboard made with different trees. For instance, the silver birch tree creates a dark colour, while the spruce produces a light brown colour.
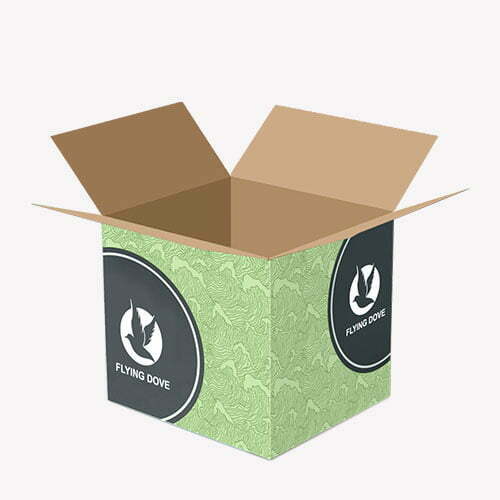
- The Pulp
Wood chips are made as soon as a tree is felled. These chips are then broken down into pulp.
Here are two methods you can use to accomplish this: You can grind the wood against a stone or you can chemically treat the wood chips.
As mentioned above, you can strengthen pulp by adding chemicals such as sodium sulphate. Most cardboard is left in its natural state, without any additional colouring. But it can also be bleached to make it appear white.
- Corrugation
After the pulp has dried, the process of cardboard making starts. Corrugated cardboard is composed of two pieces of paper or card glued together and wrapped in an outer layer of fluted cardboard.
The fluting creates a stronger structure and provides a higher level of protection against damage. Fluting involves ruffling up the paper by pressing it between two rollers with a pattern of parallel ridges cut into them.
The better the quality of the box being made, the greater the amount of fluting required. By increasing the fluting, you make boxes stronger. This is how people make high-quality boxes.
If you choose a less expensive fluting option, less material will be used, which can help make your boxes more space efficient and reduce the amount of waste generated.
- Cutting
Now that you have a full sheet of corrugated cardboard, it is time to cut the sheet to size. It completely depends on the box requirements.
The machines in the factories can automatically cut cardboard to specific sizes, depending on the production demand.
Once the basic shape of the card has been cut, it is sent to a machine called a trimmer. It adds details and flaps to make a box that can be assembled into a finished product.
In addition, the scoring makes folding the cardboard easier when the box is ready for assembly.
- Assembly
Assembly of the box will vary depending on its requirements. For businesses who want to construct their boxes on demand, using flaps and slots may be the best option.
Additionally, boxes made with tape are quick and easy to construct when needed. Generally, for robust boxes, glue and stitching are used to fold the various parts together and keep the box intact. A machine that constructs boxes on demand is available to specific box manufacturers.
For instance, Ribble Right Size is a machine that makes cardboard boxes. It allows you to choose the right size box to reduce waste and ensure a good fit.
Ready-to-use boxes can save a lot of valuable time in your production line. Once assembled, leftover pieces can be recycled and reused to make more boxes.
When boxes have served their purpose and been discarded, they can be recycled and transformed into new boxes.
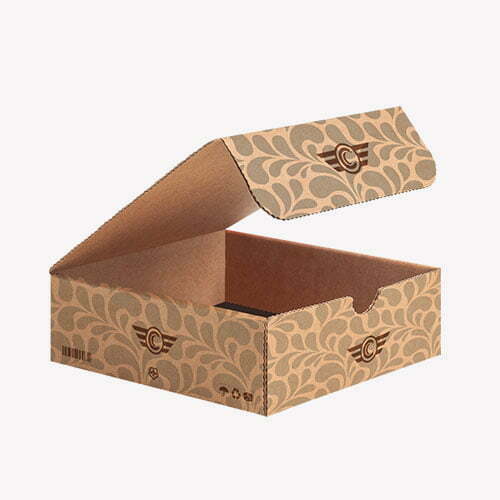
Five Tips Before You Decide on Custom-Made Cardboard Boxes
What should you consider when choosing cardboard boxes for packaging? And what factors should be taken into account when making this type of order?
First and foremost, you must define your needs clearly. If you keep these below-mentioned five points in mind when ordering custom boxes, you will always be satisfied with the results.
- QUOTATION
- NUMBER OF BOXES
- SIZE
- INTERNAL CONDITIONING
- MANIPULATION OF THE PACKAGING
Firstly, you need to decide how much money you want to spend on boxes and what quantity of boxes you need. You can then consider whether ordering more boxes is a cost-effective way to lower each unit’s price.
Secondly, the client must be clear about how they plan to use the boxes. In other words, they need to determine what product they are packaging, how heavy it is, whether it’s solid or liquid, its dimensions and so on.
Cardboard is the ideal material for protecting fragile products or products that may have problems due to sun exposure, humidity, etc. Cardboard is a good choice for packaging perishable goods, or those that are susceptible to external elements.
You must also consider the internal conditioning of the box. It is important to know if the product will be packed or loose, if it is fragile or very fragile, etc.
When transporting a product, it is necessary to consider how the packaging and filling will protect the item from rough handling.
When you place an order for custom cardboard boxes, the handling of the packaging is also something to consider. The way they are handled influences the strength of the cardboard we need.
Conclusion
It is important to note that cardboard is an earth-friendly reusable material that saves both energy and waste, as it is easily recycled.
If you are interested in learning more about our cardboard box manufacturing process or want to order one, contact one of our box manufacturers today.